Claranor nous présente en exclusivité sa dernière solution de stérilisation grâce à la lumière pulsée.
L'entreprise Claranor, spécialisée dans la décontamination de surfaces via la technologie de la lumière pulsée, a présenté à l'Anuga Foodtech sa dernière solution de stérilisation.
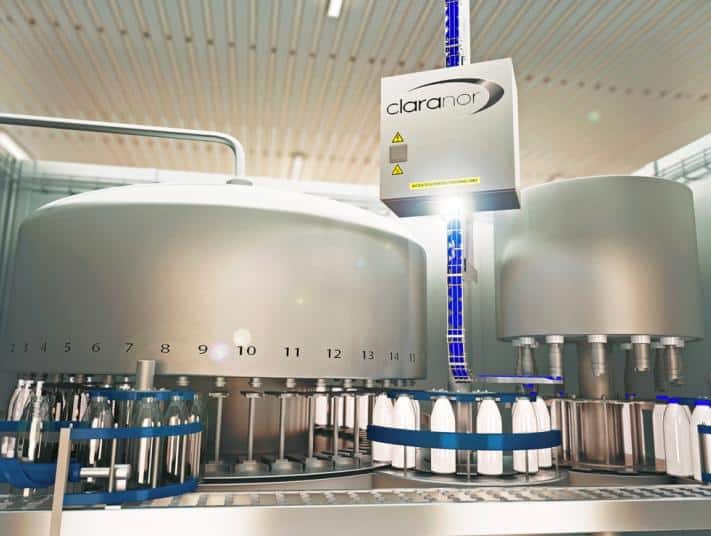
L’entreprise Claranor, spécialisée dans la décontamination de surfaces via la technologie de la lumière pulsée, a présenté à l’Anuga Foodtech sa dernière solution de stérilisation.
Agro-media.fr a interviewé pour vous Morgane Busnel, la responsable marketing et communication de la société. Elle nous présente en exclusivité l’entreprise, les produits qu’elle propose et sa dernière innovation présentée à l’occasion du salon.
Pourriez-vous nous présenter Claranor et votre rôle au sein de l’entreprise ?
« Je suis responsable marketing et communication au sein de Claranor. L’entreprise a été créée en 2004 avec pour but de proposer des solutions de décontamination des surfaces en utilisant la technologie de la lumière pulsée. Peu à peu, l’entreprise s’est focalisée sur l’application de la technologie pour le traitement des emballages. Il s’agit en effet de l’application la plus simple, étant donné que les emballages présentent des formes régulières et qu’il n’y a pas les mêmes contraintes réglementaires par rapport à l’utilisation de technologies innovantes comme il y en aurait pour les denrées alimentaires. Claranor commercialise des équipements à destination principalement des industries agroalimentaires pour le traitement des emballages et en particulier des bouchons, des pots et aujourd’hui aussi des opercules. »
Qu’est-ce que la lumière pulsée ?
« La technologie de la lumière pulsée consiste à appliquer des flashs de lumière intense riche en UV de durée très courte et de forte intensité sur des surfaces. L’effet des UV et la puissance du flash entraînent la destruction des micro-organismes. C’est une technologie qui n’agit que sur les surfaces, elle n’agit pas en profondeur du produit. »
A quelle étape du process la technologie doit-elle être utilisée ?
« En ce qui concerne les bouchons, il s’agira d’intégrer l’équipement Claranor juste au-dessus de l’étape de bouchage des bouteilles, par exemple, pour supprimer la contamination qu’il peut y avoir à l’intérieur des bouchons. On s’assure ainsi qu’il n’y aura pas de transmissions de contaminants du bouchon vers le produit.
Pour les pots, il s’agira de les traiter juste avant leur remplissage, quand ils sont encore vides.
Enfin, pour les opercules, il faudra les traiter juste avant qu’elles ne soient apposées sur le pot. »
Quel est le profil de vos clients ?
« La technologie est utilisée par exemple par des industriels qui ne souhaitent plus utiliser de chimie sur leur ligne ou qui ont déjà testé les UV continus et qui ont estimé qu’ils n’avaient pas donné des résultats suffisamment performants. Le fait que dans la lumière pulsée les UV soient appliqués sous forme de flash permet d’augmenter largement l’efficacité du traitement par rapport à un traitement continu d’une lampe à UV où elle sera beaucoup moins forte. »
Cette technologie peut-elle être adaptée sur des lignes à haute cadence ?
« Oui, bien sûr. En général, dans les conditions industrielles, la technologie de la lumière pulsée permet de réduire de plusieurs log (terme microbiologique) les contaminations de moisissures ou de bactéries. Nous faisons des tests avant la mise en place des machines afin d’estimer quelle puissance régler en termes de nombre de flashs. En général, on ne dépasse pas deux à trois flashs par emballage. Etant donné que ce sont des flashs qui ne durent que quelques centaines de microsecondes, ils peuvent être appliqués en moins d’une seconde, ce qui permet d’intégrer l’équipement dans des lignes sans en modifier la cadence. La technologie est donc tout à fait compatible avec des cadences industrielles. Pour des lignes d’embouteillage, nous pouvons aller jusqu’à 80 000 ou 90 000 bouchons traités par heure. Pour les pots, nous pouvons atteindre 40 flashs par minute. Nous n’avons jamais rencontré de problèmes à cause de la cadence de production des lignes. »
Quels sont les avantages et les inconvénients de cette technologie ?
« Les inconvénients, d’abord. C’est une technologie de surface et il faut donc que toute la surface qui doit être traitée soit exposée aux flashs. Cela implique par exemple que s’il y a des phénomènes d’ombre sur une surface d’emballage ou de tout autre produit qui doit être traité, cela peut altérer l’efficacité de la technologie. La lumière doit pouvoir traiter toute la surface de façon directe ou grâce à des phénomènes de réflexion. C’est la seule limite de la technologie.
En termes d’avantages, il s’agit d’abord une alternative au traitement chimique. Nos équipements sont extrêmement compacts et peuvent très facilement être intégrés sur des lignes déjà existantes, ils ne nécessitent pas de modification de ligne. Par exemple, les coffrets pour le traitement des bouchons s’installent juste au-dessus de la boucheuse. Le traitement n’utilise pas d’eau, il consomme donc très peu d’énergie en comparaison d’une stérilisation globale de ligne. Il n’y a pas de temps de préchauffage, de préparation de produits avec de l’eau, etc. En termes de logistique, c’est une solution simple et compacte, à sec et sans chimie. La technologie est ce que l’on appelle « Cleantech », c’est-à-dire écologique. »
A ce jour, combien d’entreprises ont choisi cette technologie de stérilisation ?
« Aujourd’hui, nous avons un peu plus de 50 installations dans le monde entier. La majorité des installations sont faites sur des lignes d’embouteillage, donc sur le traitement de bouchons. Cependant, le traitement des pots commence à se développer depuis un an ou deux. Le traitement des opercules, quant à lui, est réellement nouveau et devrait se développer dans les mois à venir. »
Vous avez lancé à l’Anuga Foodtech la première solution de stérilisation pots/opercules. En quoi consiste-t-elle ?
« Dans le principe, elle est très proche de la stérilisation des bouchons et des pots. Nous avons adapté la technologie pour pouvoir associer plusieurs lampes afin de traiter un nombre de pots ou d’opercules indéfini. Il n’y a plus de limitation en termes de largeur de traitement. Pour le traitement des pots, l’équipement de Claranor se positionnait juste au-dessus de la ligne. Pour le traitement des opercules, c’est quasiment le même coffret optique mais il va être placé à la verticale et va flasher l’opercule juste avant qu’il soit apposé. »
Quel retour sur investissement un industriel peut-il espérer grâce à cette solution ?
« Je ne peux pas vous donner de chiffre exact, mais je peux vous dire que pour la solution opercule l’avantage de la technologie est avant tout d’apporter une alternative aux traitements chimiques ou aux traitements sous UV continus. Il y a clairement un gain de place. »
Agro-media.fr remercie Mme Morgane Busnel pour avoir accepté de répondre à nos questions.
Pour en savoir plus sur Claranor, n’hésitez pas à consulter leur site web.
Propos recueillis par Vanessa Dufus.
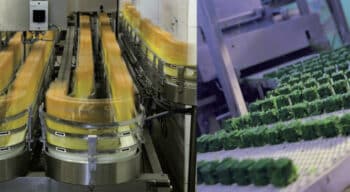
Dans le cadre de la loi du 8 novembre 2019 relative à l’énergie et au climat, la France s’est fixé comme objectifs de …
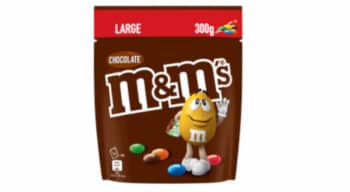
Dans le cadre de ses engagements en faveur d’emballages circulaires, Mars Wrigley France lance un projet pilote d’éco-conception de son pochon M&M’s Choco …
Forum Labo 2025 : 5 analyseurs dédiés aux laboratoires du secteur agroalimentaire
À quelques jours de l’ouverture du Forum Labo 2025, organisé par RX France sous l’égide du Comité Interprofessionnel des Fournisseurs du Laboratoire (CIFL), …
Forum Labo 2025 : 3 solutions innovantes pour la sécurité et les performances des laboratoires dans l’agroalimentaire
Sécurité et performances des laboratoires feront partie des maîtres-mots du Forum Labo 2025, la filière des laboratoires de R&D qui fait son grand …
Forum Labo 2025 : L’événement incontournable de la filière des laboratoires de R&D fait son grand retour à Paris
Le Forum Labo, manifestation du CIFL (Comité Interprofessionnel des Fournisseurs du Laboratoire) organisée par RX France, s’apprête à investir la Porte de Versailles …
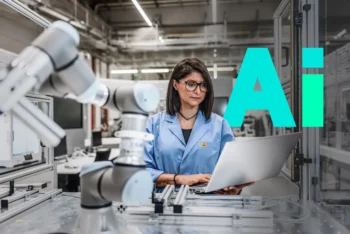
Confrontée à des défis majeurs tels que la gestion de la demande, l’optimisation des chaînes de production et l’amélioration de la qualité des …
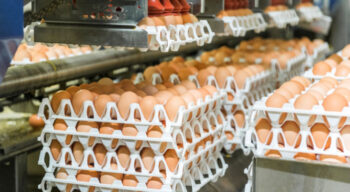
L’œuf n’a jamais été aussi prisé par les Français ! En 2023, la consommation moyenne par habitant a atteint 224 œufs, un record …
Top 10 des cabinets de recrutement agroalimentaire
Dans l’agroalimentaire, la performance passe aussi par la qualité des recrutements. Pour structurer des équipes solides et opérationnelles, les entreprises ont tout intérêt …
TOP 10 des entreprises de marquage industriel pour l’agroalimentaire
Le marquage industriel est un élément central pour les acteurs de l’agroalimentaire. Il permet d’identifier les produits avec précision, de sécuriser leur traçabilité …
A quoi ressemblera l’industrie agroalimentaire française à l’horizon 2040 ?
A quoi ressemblera l’industrie agroalimentaire française à l’horizon 2040 ? C’est la question à laquelle a tenté de répondre le Conseil général de …