Chaleur : comment la récupérer et la valoriser
La récupération de la chaleur est l'une des techniques les plus utilisées par les IAA pour optimiser leurs performances énergétiques. Tour d'horizon des différentes possibilités.
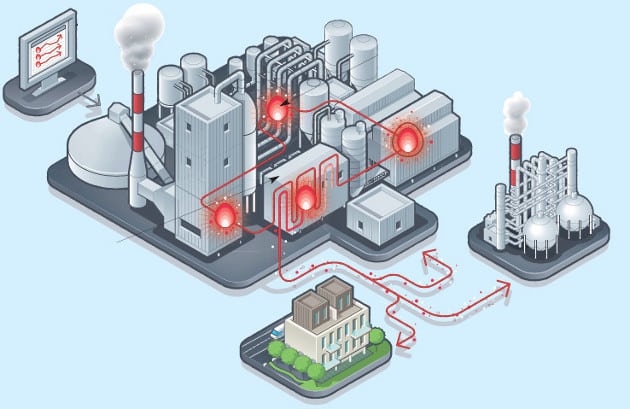

Selon l’Ademe, la chaleur perdue par l’industrie en France représente un gisement de plus de 100 TWh, donc 60 %, à plus de 100°C. Les principaux secteurs concernés par ces pertes sont la chimie, la plasturgie, le papier, les métaux, mais aussi l’agroalimentaire.
Valoriser cette chaleur perdue représente ainsi un enjeu stratégique pour les IAA, afin d’augmenter les performances énergétiques des sites et des procédés et de réduire leur impact environnemental.
D’ailleurs, selon Okavango-energy, la majorité des industriels (53 %) ont déjà mis en place au moins un équipement de récupération de chaleur sur leurs installations de façon ponctuelle. Mais seul 13 % ont réalisé un bilan global des puits et sources de chaleur.
Il existe plusieurs façons, pour les IAA, de récupérer la chaleur.
Récupération de chaleur avec un échangeur de chaleur
Dans ce cas de figure, la chaleur est transférée à d’autres fluides, procédés ou stockages, tels que le chauffage des locaux ou d’autres flux sur site. Les équipements utilisés ont l’avantage d’être fiables, robustes, de résister à des pressions élevées, ainsi qu’à de grands écarts de température. Ils sont par contre assez encombrants, et moins performants que d’autres types d’échangeurs.
Récupération de chaleur en relevant la température
Les industriels ont pour cela recours à une pompe à chaleur électrique ou à gaz. Cette technique permet de récupérer la chaleur contenue dans des effluents à basse température, pour un usage à un niveau de température supérieur. En pratique, un fluide frigorigène circule en boucle fermée à travers un évaporateur, un compresseur, un condenseur et un détenteur, et passe successivement de l’état de liquide à celui de gaz. Cela permet de récupérer de l’énergie à basse température, en évitant les rejets et peut remplacer partiellement une chaudière. La consommation d’électricité est néanmoins élevée, tout comme l’investissement et le niveau de maintenance nécessaire. Ces équipements sont souvent utilisés dans l’agroalimentaire, où les rejets et les besoins en eau chaude sont nombreux.
Récupérer la chaleur en abaissant la température
Grâce à une machine à absorption ou à adsorption, il est possible de produire du froid à partir de l’énergie récupérée sur un effluent chaud. Le principe : dans un système par absorption, une source de chaleur est utilisée pour séparer un constituant volatil d’une solution. Ce constituant séparé sous phase vapeur est ensuite condensé, puis détendu. Le liquide issu de la détente s’évapore, absorbant ainsi de la chaleur et produisant du froid. Ces machines sont particulièrement fiables et silencieuses. L’investissement nécessaire est par contre conséquent. Et cette technique oblige à utiliser des fluides toxiques et inflammables.
Récupérer la chaleur en le transformant en une autre forme d’énergie
L’utilisation de fluides actifs, tels que la vapeur, transforme la chaleur stockée, sous forme moléculaire, qui peut ensuite être utilisée ou convertie en énergie électrique. En pratique, la chaleur contenue dans les effluents gazeux est utilisée pour chauffer et vaporiser à haute pression un fluide organique appelé fluide de travail. Le fluide organique ainsi vaporisé est détendu dans une turbine. Le passage du fluide organique permet de produire de l’électricité. Les grandes possibilités de choix en matière de fluide de travail permettent de valoriser des effluents à partir de 80 °C et jusqu’à 350 °C. La maintenance et la supervision sont limitées sur ce type d’équipements. Mais les rendements électriques restent modestes.
Récupérer la chaleur en la stockant pour une utilisation ultérieure sur le site
L’énergie peut être récupérée sous forme de chaleur ou de travail mécanique, qui peut éventuellement être transformé en électricité ou être utilisé pour rehausser le niveau de température d’une autre source de chaleur. Cette technique a l’avantage de pallier au décalage entre la production de chaleur fatale et les besoins en chaleur sur le site. Encombrement et pertes d’énergie font partie des inconvénients.