Des équipements plus performants et économes pour réduire la consommation énergétique dans l’industrie agroalimentaire
L’industrie agroalimentaire, particulièrement gourmande en énergie, a vu l’apparition d’une nouvelle génération d’équipements conçus pour réduire la consommation d’énergie tout en optimisant la productivité. Ces machines, principalement utilisées dans les processus de chauffage, de refroidissement et de conditionnement, bénéficient aujourd’hui d’innovations majeures, telles que des moteurs à haut rendement et des systèmes de récupération de chaleur, permettant une gestion …
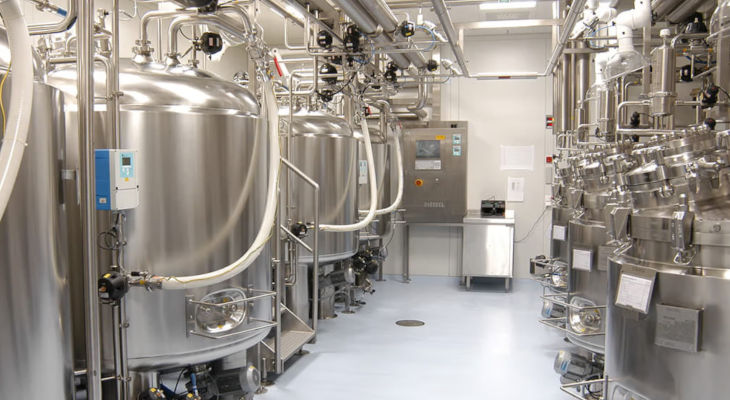
L’industrie agroalimentaire, particulièrement gourmande en énergie, a vu l’apparition d’une nouvelle génération d’équipements conçus pour réduire la consommation d’énergie tout en optimisant la productivité. Ces machines, principalement utilisées dans les processus de chauffage, de refroidissement et de conditionnement, bénéficient aujourd’hui d’innovations majeures, telles que des moteurs à haut rendement et des systèmes de récupération de chaleur, permettant une gestion énergétique plus intelligente. Voici quelques exemples d’équipements innovants adoptés par des entreprises du secteur.
Les compresseurs à vitesse variable : Les compresseurs sont essentiels dans les processus de refroidissement et de réfrigération, mais aussi parmi les équipements les plus énergivores. Des entreprises comme Atlas Copco ont mis au point des compresseurs à vitesse variable, capables d’adapter automatiquement leur puissance en fonction des besoins réels du processus de production. Cela permet d’éviter une surconsommation d’énergie pendant les périodes de faible demande. Grâce à cette technologie, Nestlé a pu réduire de 35 % la consommation d’énergie de ses systèmes de compression dans ses usines de transformation de lait.
Les systèmes de récupération de chaleur : L’ingénierie thermique est un domaine où les économies d’énergie sont considérables. Un exemple marquant est l’utilisation des systèmes de récupération de chaleur. Tetra Pak, par exemple, a développé des échangeurs thermiques capables de capter la chaleur produite lors du traitement thermique des aliments et de la réutiliser pour chauffer d’autres parties du processus de production. Cette approche a permis à des entreprises comme Danone de réduire de 20 % leur consommation de vapeur dans certains sites de production de produits laitiers.
Une gestion énergétique plus intelligente
Les fours à haute efficacité énergétique : Les fours utilisés pour la cuisson des produits agroalimentaires consomment énormément d’énergie. La société Baker Perkins a développé une gamme de fours économes en énergie qui utilisent des systèmes de récupération de chaleur pour réutiliser l’énergie des gaz d’échappement et la réinjecter dans le cycle de production. Grupo Bimbo, l’une des plus grandes entreprises de boulangerie, a adopté cette technologie, réduisant ainsi de 15 % la consommation d’énergie de ses usines.
Les systèmes de refroidissement automatisés : Les équipements de réfrigération représentent une part importante des dépenses énergétiques dans l’industrie agroalimentaire. L’automatisation de ces systèmes, combinée à des technologies de surveillance en temps réel, permet de mieux gérer les températures en fonction des besoins précis. GEA Group, un acteur majeur dans le domaine du froid industriel, a développé des systèmes de refroidissement intelligents capables de moduler leur consommation en fonction des pics de production, évitant ainsi une surutilisation. Ces systèmes ont été adoptés par PepsiCo, qui a enregistré une baisse de 25 % de sa consommation énergétique dans ses centres de production de boissons.
Les systèmes de conditionnement économes : Le conditionnement est une étape cruciale qui nécessite une gestion fine de l’énergie. Ishida, leader dans les solutions de pesage et d’emballage, a développé des équipements de conditionnement à haute efficacité énergétique, capables d’optimiser la quantité de matière utilisée tout en réduisant les besoins en électricité pour le fonctionnement des machines. Unilever a intégré ces technologies dans ses lignes de conditionnement de produits alimentaires, réduisant ainsi leur empreinte carbone.
Vous l’aurez compris, l’optimisation de la consommation énergétique dans l’industrie agroalimentaire passe par l’adoption d’équipements plus performants, capables de moduler leur consommation en fonction des besoins réels. Grâce à des innovations comme les compresseurs à vitesse variable, les systèmes de récupération de chaleur ou les technologies de refroidissement automatisées, les entreprises peuvent réaliser des économies significatives tout en respectant les exigences environnementales.