La maintenance prédictive, une valeur ajoutée pour l’industrie alimentaire
Réactive, préventive ou prédictive ? Quelle maintenance adopter ? Dans la majorité des cas, les pièces des équipements sont réparées lorsqu’il y a une panne par les opérateurs de machines. Il s’agit de la maintenance réactive. L’intervention nécessite du temps et parfois un arrêt de production plus ou moins long. Afin d’éviter ces temps morts, la maintenance prédictive permet de prévenir …
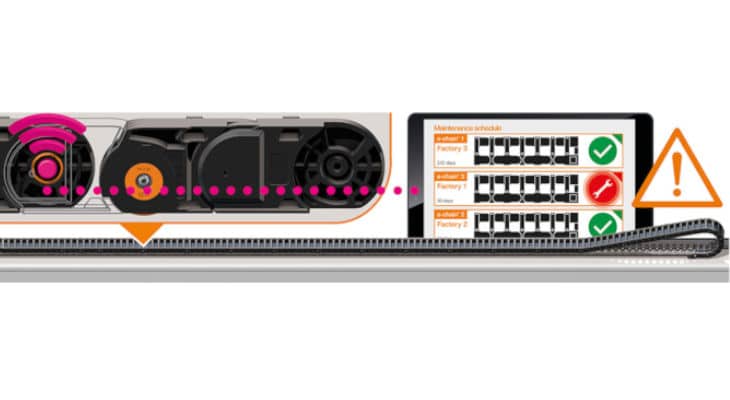
Réactive, préventive ou prédictive ? Quelle maintenance adopter ? Dans la majorité des cas, les pièces des équipements sont réparées lorsqu’il y a une panne par les opérateurs de machines. Il s’agit de la maintenance réactive. L’intervention nécessite du temps et parfois un arrêt de production plus ou moins long. Afin d’éviter ces temps morts, la maintenance prédictive permet de prévenir les pannes, et par conséquent de prévoir ces défaillances et donc de faire des économies durant la production. Comment ? Grâce à des systèmes intelligents capables de reconnaître les dysfonctionnements avant qu’ils ne se manifestent. Les données de productions sont ainsi analysées permettant d’identifier des modèles et prévoir les problèmes potentiels.
La maintenance préventive consiste quant à elle à effectuer des mesures de maintenance à des intervalles donnés. Ces derniers peuvent être fixés en fonction d’une durée de production ou d’un nombre de pièces produites. Il s’agit donc de ne plus attendre la défaillance des installations ou des pièces de machine mais bien d’effectuer systématiquement des inspections et des opérations de maintenance à titre préventif.
Véritable stratégie de maintenance, la maintenance prédictive collecte pendant la production des données liées aux processus et à la machine par des capteurs et des interfaces, qui sont enregistrées, puis analysées. Cette mise en réseau des machines et des informations en temps réel rend la maintenance prédictive incontournable pour les industriels dont chaque immobilisation ou panne a un coût significatif. La maintenance prédictive permet ainsi de générer des économies par rapport à la maintenance préventive. Les explications avec des experts (liste non exhaustive) du sujet !
L’Internet des objets, un élément clé du processus
«Dans les usines de production, l’utilité de la maitenance prédictive permet plusieurs économies de coûts puisqu’elle permet de détecter la panne avant qu’elle ne se produise», explique l’expert BoshRexroth, «cela permet ainsi de réduire la fréquence à laquelle la maintenance d’une machine est effectuée et d’éviter une maintenance réactive imprévue sans entraîner de coûts élevés liés à une maintenance trop importante. La maintenance prédictive utilise des outils de surveillance pour évaluer les performances d’un équipement en temps réel. L’Internet des objets est ainsi un élément clé de ce processus. Il permet à différents équipements et systèmes de se connecter, de travailler ensemble et de partager, d’analyser et de traiter des données». A cet effet, des capteurs de maintenance prédictive pour capturer des informations sont utilisés. Parmi les exemples d’utilisation de capteurs de maintenance prédictive figurent l’analyse des vibrations, l’analyse de l’huile et l’imagerie thermique. «Les entreprises peuvent s’aider de la gestion de la maintenance assistée par ordinateur (GMAO). Cet outil permet d’aider à la prise de décision en fournissant des informations clés concernant la maintenance de machines. Ces logiciels de supervision permettent d’éviter les incidents et l’arrêt imprévu d’une ligne de production. Couplée avec l’Internet des objets, la GMAO fournit un flux de données constant permettant d’analyser les données afin de surveiller et de maintenir les machines en bon état de marche», explique l’expert BoshRexroth.
«La maintenance prédictive est une grande valeur ajoutée particulièrement pour l’industrie agroalimentaire», confirme de son côté Instrumentys, expert dans les instruments de mesure. «La contribution de la maintenance prédictive s’étend à toutes les industries, mais dans l’industrie alimentaire, elle révèle une valeur ajoutée, qui a une importance particulière dans le produit final». Pour Instrumentys, la méthodologie de maintenance des machines de production industrielle est effectivement un élément essentiel, dans l’atteinte des objectifs de performance. A cet égard la surveillance continue est nécessaire à l’optimisation des interventions de maintenance. «Parmi les modèles de maintenance les plus connus de l’industrie, la maintenance prédictive se traduit par une nouvelle utilisation des données, collectées sur les machines et leurs environnements. Comme son nom l’indique, ce modèle est basé sur la prédiction de l’occurrence de scénarios ou d’éventuelles pannes susceptibles d’interférer avec le fonctionnement normal de l’ensemble de la chaîne de production», explique l’expert, «Or la réglementation actuelle de l’industrie alimentaire vise à garantir que le produit final respecte les normes de qualité requises. De fait la modernisation des équipements de production a permis d’augmenter la capacité de production et l’efficacité. Cependant, la complexité des processus signifie souvent une augmentation importante des temps d’arrêt inhérents aux pannes et à la maintenance des équipements. Aussi la surveillance de l’état des équipements a une pertinence supplémentaire. Parce que c’est de là que viennent les données nécessaires pour définir et programmer les interventions de maintenance prévisionnelles. Surtout avec le moins d’impact possible sur le niveau des ressources, que ce soit au niveau mécanique ou le moment opportun de l’intervention technique».
L’arrêt d’une ligne de production dans l’industrie alimentaire est clairement différent de l’arrêt d’une ligne de production de produits non périssables. «Bien que la sécurité soit une priorité dans ces deux scénarios. Si la production des pièces est en arrêt, il n’y aura pas de détérioration des pièces jusqu’à ce que l’équipement revienne à son fonctionnement normal. Et les pertes n’incomberont qu’au temps d’arrêt de la production. Lors de l’arrêt d’une unité de production alimentaire, les ingrédients peuvent changer, mettant en péril la qualité du produit final. Et entraînant des pertes tant en termes de produit qu’en temps de production. Plus qu’affecter la qualité des produits, cela affectera l’expérience du consommateur et, dans des situations plus complexes, impliquera des problèmes juridiques avec les marques et les distributeurs», explique Instrumentys qui propose une solution moderne pour rentrer dans l’ère de l’industrie 4.0 : Les solutions sans fil PLUS de Tekon Electronics ont rationnalisé les stratégies de collecte de données dans l’industrie agroalimentaire. Secteur où des variables telles que la température, HR, la vitesse, les vibrations, la pression, sont incontournables au processus. En conséquence ces dernières peuvent affecter la qualité du produit. Elles permettent ainsi une plus grande visibilité des points de référence dans l’infrastructure.
«Avec l’émergence de la nouvelle révolution industrielle, l’IloT, la numérisation des process est favorisée par des capteurs et équipements. Ceux-ci assurent la collecte et le stockage des données localement (edge computing) ou, plus souvent, dans le cloud. De surcroît la convergence vers les solutions cloud permet une meilleure connectivité des utilisateurs et une plus grande sécurité des informations. Donnant un accès aux plates-formes et aux données, quels que soient l’emplacement des appareils et des utilisateurs. Les plateformes IoT deviennent de plus en plus une réalité, où la visualisation graphique des données et le composant de surveillance sont mis en évidence pour l’utilisateur. La Plateforme IoT de Tekon Electronics, permet la collecte, le traitement, la visualisation et l’analyse avancée des données. Favorisant une prise de décision affirmée, concernant la planification des événements de maintenance », commente l’expert pour qui la maintenance prédictive est un exemple clair de la manière de préparer et structurer les données en vue d’une assimilation. Et ceci par les applications d’apprentissage automatique (machine learning) et d’intelligence artificielle.
Une maintenance prédictive au plus près des besoins du client
«Par maintenance prédictive, on entend en règle générale l’anticipation d’une anomalie et la prévention de celle-ci sur un équipement de machine ou sur des composants grâce à des données relatives à son/leur état(s). Elle utilise pour cela des méthodes basées sur les données qui analysent l’état de vos machines et qui vous aident à prédire des dysfonctionnements, des perturbations ainsi que le moment où des tâches d’entretien devront être effectuées », explique igus qui propose pour la maintenance prédictive son module i.Cee ( « je vois »), un concept qui trouve maintenant aussi sa place dans les environnements réseau et les concepts IoT de ses clients.
En effet, la possibilité d’intégration totale dans les environnements réseau prévus à cet effet des différentes applications ouvre la voie à la réalisation de cas d’utilisation extrêmement variés d’industrie 4.0. «Tout est possible, de la gestion préventive de la maintenance qui planifie les entretiens réguliers en fonction de l’utilisation à la gestion globale des données des capteurs qui permet même l’intégration de solutions cloud de tiers en passant par la gestion des anomalies délocalisée qui communique immédiatement toute modification imprévue par différents canaux mobiles.Toutes les informations sont agrégées dans un tableau moderne, en ligne ou hors ligne dans le réseau local, selon les souhaits du client. Ce module i.Cee:plus de 2ème génération est donc la pièce maîtresse de tout système de chaînes porte-câbles utilisé dans l’industrie 4.0, avec pour objectif constant d’obtenir le maximum de sécurité pour les équipements et l’utilisateur et une durée de vie aussi longue que possible du produit», explique igus.
De quoi a-t-on besoin pour mettre en œuvre une maintenance prédictive ? Celle-ci nécessite la mise en place de différents capteurs afin de collecter des données importantes pour le fonctionnement de la machine, par exemple régimes, température, niveau sonore, vibrations des paliers ou consommation d’énergie. Les données de ces capteurs doivent ensuite être interprétées et correctement évaluées. «On a besoin pour cela d’une technologie d’analyse en temps réel combinée à une banque de données. Une fois que l’on dispose du tout, il est possible de remédier au problème sur une machine avant qu’il ne se produise vraiment », explique l’expert igus.
Toujours selon ce dernier, selon des études de cabinets de conseil tels McKinsey et Accenture, la maintenance prédictive pourrait permettre entre 50 et 70% d’immobilisations imprévues en moins et des économies de 20 à 40 % au niveau des coûts d’entretien. Le cabinet Roland Berger affirme quant à lui avoir découvert que la maintenance prédictive faisait baisser à 15 % le temps consacré à l’entretien, qui était de 40 % avec la maintenance réactive classique. Si les avantages de la maintenance prédictive sont nombreux et évidents, «le coût de l’investissement ponctuel dans des capteurs et dans un logiciel d’analyse et d’évaluation des données reste important», explique igus qui propose les plastiques intelligents igus i.Cee afin de permettre de réduire ceux-ci à un minimum.
GE Digital de son côté propose la solution logicielle de maintenance prédictive SmartSignal de GE Digital qui comprend des analyses de prévision « Time-to-Action ». Ses nouvelles fonctionnalités incluent des analyses de temps d’action uniques pour prévoir quand un dysfonctionnement peut se produire, des outils de visualisation et d’analyse améliorés et l’expansion continue du Digital Twin Analytics et du catalogue de contenu couvrant plus de 300 classes d’équipements industriels parmi les fabricants. “GE Digital SmartSignal est une solution logicielle de maintenance prédictive de premier plan dans tous les secteurs depuis près de deux décennies, avec un investissement continu dans l’étendue de l’analyse et l’innovation. Alors que d’autres solutions peuvent ne fournir qu’une indication générale d’un problème, SmartSignal diagnostique la cause et la gravité du problème et détermine le délai requis pour la résolution”, affirme GE Digital.